-
Uses high-performance pulse nozzle
-
Advanced simulation technology
-
Reduce die lubricant usage
-
Reduce air blow time
-
Improve cycle time
-
Reduce environmental footprint
-
Decrease on-site setup time
-
Compatible with oil-based or water-based lubricants
-
Has a track record in die casting machines of 150t to 3500t
-
Over 300 units installed worldwide

EcoShot Nozzle
Achieve unprecedented pulse speed with our solenoid nozzle
Improved External Cooling
Suppression of the Leidenfrost Effect
With competing continuous spray systems that use water-based lubricants, die casters often experience poor external cooling effects and subpar lubricant adhesion. Water evaporates upon contact with the high-temperature die, forming a gas that acts as a barrier between die lubricant and the mold. This barrier of evaporated water prevents lubricant adhesion and is known as the Leidenfrost effect. The surface temperature of the mold must gradually converge with the Leidenfrost point 193 °C (379 °F) before lubricant can finally adhere. Such drastic heating and cooling takes time, and can cause damage to the die over repeated cycles. Significant quantities of water-based lubricant are used to cool the die before finally forming lubricant film, resulting in a large quantity of waste.
With EcoShot's rapid pulse spray, external cooling effects are improved through mitigation of the Leidenfrost effect. Though rapid pulsing of lubricant spray, water is allowed to fully evaporate before applying additional lubricant, which prevents a gaseous barrier from forming. As the barrier is not able to form, EcoShot's pulse spray improves lubricant adhesion, even at higher die temperatures. With this rapidly repeated process of spraying and evaporation, external die cooling becomes faster and requires less die lubricant. Cycle time decreases due to the unprecedented 0.01 second pulsations and lubricant quantity is drastically reduced.
EcoShot Pulse Spray
Need concrete data? We have conducted an experiment to see how spray patterns affect die temperature lubricant quantity. With Ecoshot's pulse spray, the amount of lubricant usage and wastewater is significantly reduced, and improved die cooling is observed.

A
B

A
B

A
B

A
B
Before Spraying
Continuous Spray
EcoShot Pulse
EcoShot Rapid Pulse
Temperature
A… 309.88 ℃
B… 311.29 ℃
1 second after spraying
A… 261.99 ℃
B… 272.01 ℃
1 second after spraying
A… 253.34 ℃
B… 273.73 ℃
1 second after spraying
A… 232.23 ℃
B… 253.93 ℃
Cycle Time
3.5 sec.
3.5 sec.
3.5 sec.
Spray Pattern
Spray... 3.5 sec.
Stop... None
Spray... 0.5 sec. X 4 times
Stop... 0.5 sec. X 3 times
Spray... 0.25 sec. X 7 times
Stop... 0.25 sec. X 7 times
Lubricant Quantity
42cc
24cc
21cc
Observations
Significant dripping and wastewater. Poor lubricant adhesion due to Leidenfrost effect.
Improved adhesion (via mitigation of Leidenfrost effect) and reduction in wastewater. Improved cooling in certain areas.
Improved adhesion (via mitigation of Leidenfrost effect) and reduction in wastewater. Significantly improved cooling.
Results
Adhesion ... Poor
Wastewater ... Significant
Vaporization ... Small
Adhesion ... Good
Wastewater... Low
Vaporization ... High
Adhesion ... Excellent
Wastewater ... None
Vaporization ... High
Minimize Cycle Time
With EcoShot's pulses as low as 0.01 s, die casters can apply lubricants in the ideal thickness, without overlap. This enables robotic movement to be used for precise application of lubricant, optimizing the quality of your castings.
With competing pulse nozzles, nozzle response time is delayed, nozzles are not able to keep up with robot movement. Therefore, lubricant cannot be targeted to a specific point.
Thick film
EcoShot: 0.01s Interval Pulse

Even Coat
EcoShot: 0.05s Interval Pulse

Mostly Even Coat

Competing Pulse Nozzle: 0.5s Interval Pulse
Uneven Coat
No Lubricant Applied
Thin film

500msec
Pilot Air
Conventional Pulse Spray
Start Spray

500msec
Pilot Air
Stop Spray
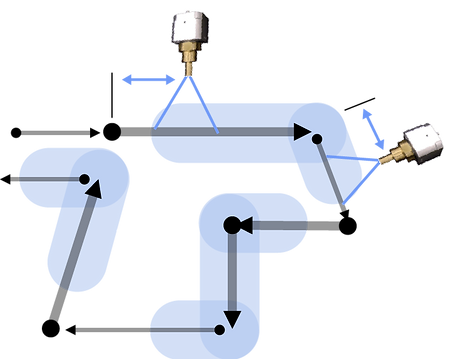
Delayed Spray
Delayed Stop
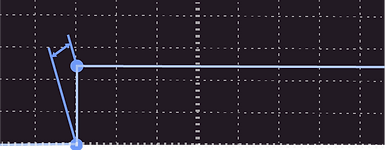
Electrical Pulse
10msec
EcoShot Pulse Technology
Start Spray

Electrical Pulse
10msec
Stop Spray

Immediate Spray Response
Immediate Stop Response
No Leakage, Reduced Clogging
EcoShot nozzles are equipped with solenoid valves to ensure leakage does not occur.
Nozzles are also self-cleaning, as air is blown between pulses to prevent clogging.
Start
Spray
Stop
Air
Lubricant
Coil
Air
Coil
Air is blown, clearing the nozzle
10ms later lubricant is sprayed
Air + Lubricant
Air only

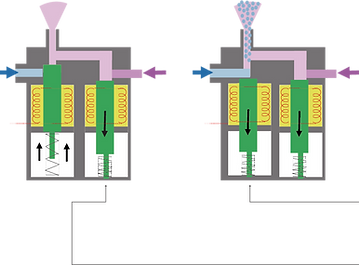
Lubricant
After stopping the discharge of the release agent
Stop the air after 10msec
Air only
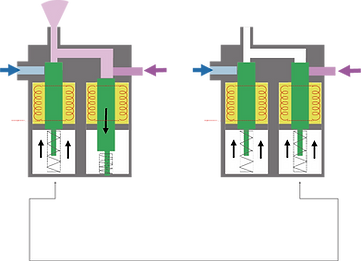
Streamlined Setup, Compact Size
Since solenoid valves are built into EcoShot nozzles, there is no need to supply each nozzle with mixing air, pilot air, and lubricant hoses. Air and lubricant supply is branched off within the spray head, allowing a streamlined setup. Only one set of hosing is required supplying air and lubricant to the robot. This simplified setup allows EcoShot to be more compact than competing die lubrication systems.
Conventional (long piping and slow response)
.png)
Pilot air travels through pipe
Valve Stand
Robot
Nozzle
Spray cassette
Lubricant Pump
Nozzle
EcoShot technology (reduced piping / minimal response time)
.png)
ON
Nozzle Valve
Electrical control
(1 multi-core cable)
Spray Stopped
Spray On
OFF
Excellent Versatility
The angle and flow rate of EcoShot nozzles can be easily adjusted by simply replacing the tip.
Oil and Water Compatible
EcoShot has a proven track record with both oil-based and water-based solutions, and also provides hybrid solutions for die casters requiring both oil and water-based lubricants.
With controlled external cooling, EcoShot allows die casters to extend the lifespan of their die. Conventional die lubrication systems cause extreme cooling of the die, which results cyclic thermal stress and shortens die life. Die casters that switch to EcoShot can control cooling to a suitable range, extending production.
Extends Die Life
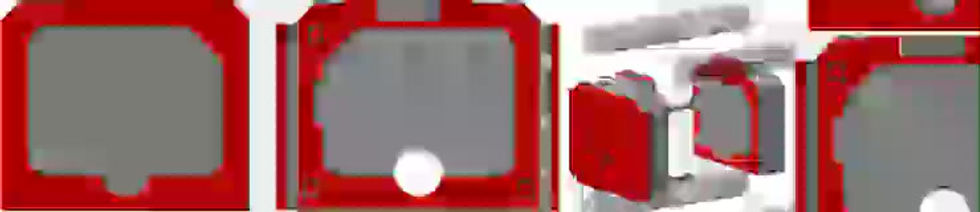
EcoShot Simulation
Simulate your spray patterns with Envision, for unparalleled control
-
Determine optimal nozzle arrangement and robotic movement
-
Test robotic movement and spray pattern before production
-
Know the cycle time in advance
-
Shortening on-site installation time
-
Plan for quality control before large-scale production
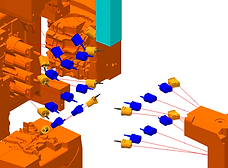

Optimize
Nozzle placement
Streamline Robotic Movement


Refine Spray
Pattern
Project and Improve
Cycle Time
Bring Simulation Results to Life
Through laser correction, EcoShot ensures correct robot positioning to bring simulation results to life.
-
Automatic adjustment of robot positioning
-
Comparison of actual robot position and simulation for maximum accuracy
-
Match actual robotic movement to simulation with ± 2 mm tolerance
-
Reduce setup time by almost 70%
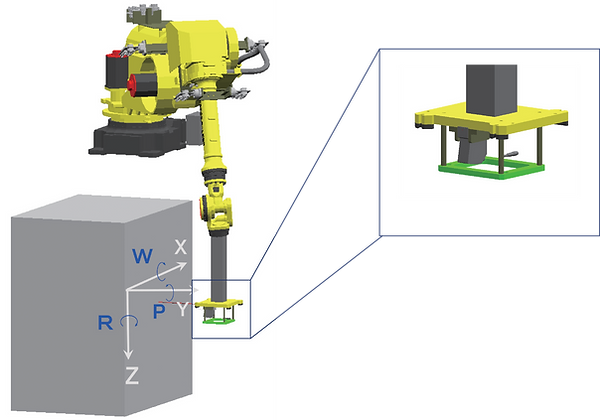
Guaranteed 2 mm tolerance
Laser correction jig
Optimize Productivity and Versatility
EcoShot allows die casters to meet their specific casting needs to optimizing the balance between productivity and versatility in die lubrication. When maximizing productivity, we focus on minimizing robot movement and increase nozzles quantity. For die casters that wish to maximize versatility, we decrease nozzles quantity and increase robotic movement.
RYOEI uses advanced simulation to optimize each spray system according to your specific needs. Through simulation of robotic movement, spray film application, and nozzle positioning, our unique capabilities can help you reach your manufacturing goals.

Low Productivity High
Good Versatility Bad
Robotic Movement
Nozzle Quantity
Low
High
Few
Several

Benefit Overview
Reduce Lubricant Quantity
-
EcoShot's Nozzle and Simulation allows die casters to apply oil and water-based lubricants with an optimized thickness and minimal dripping, reducing the amount of lubricant required
-
Maximize efficiency of external cooling and target hot spots by pairing EcoShot Nozzle with a water-based lubricant
Reduce Cycle Time
-
Reduce robot movement and optimize nozzle placement with EcoShot Simulation
-
Reduce air blow time with targeted and controlled application of die lubricant
Minimize Environmental Footprint
-
Minimize wastewater with
-
Improve workplace safety by minimizing airborne lubricant
Competing Spray Systems
EcoShot Pulse Spray
Spray process
-
Robot movement
-
Air Blow: Die Cleaning
-
Fixed spray
-
Movable spray
-
Air Blow: Lubricant Spreading
Fixed and moving spray occurs simultaneously
.png)
1
2
3
4
5
1
2
3 + 4
5
1
1
Spray cycle time
Spray cycle time